For many years the Stailer team has been working on creating
solid and reliable straps for your every day use.
We develop, manufacture and continually improve our straps.
The development process of each strap collection begins with sketching, drafting, and 3-D modelling. Then we select fitting materials from the leading leather industry manufacturers for every model.
We make strap prototypes and test them thoroughly to make sure the prospective watchstrap meets the current industry standards. We use high-precision molds and tools for the production of our watchstraps; it ensures the greatest possible quality level at each stage of the production.
There are two main functions that watchstraps serve, namely, holding a watch on the wrist and complementing the overall image of the product. We do our best to take into account both these factors while working on the design of watchstraps.
Our team constantly works on the development of new designs. This process not only implies the creation of shape and structure of the strap, but also leather selection of proper texture and color; matching lining; the selection of stitching thickness and color; buckle construction - everything to make sure the strap serves you for a long time, feels comfortable in wear and complements your watch.
Production
Technologies
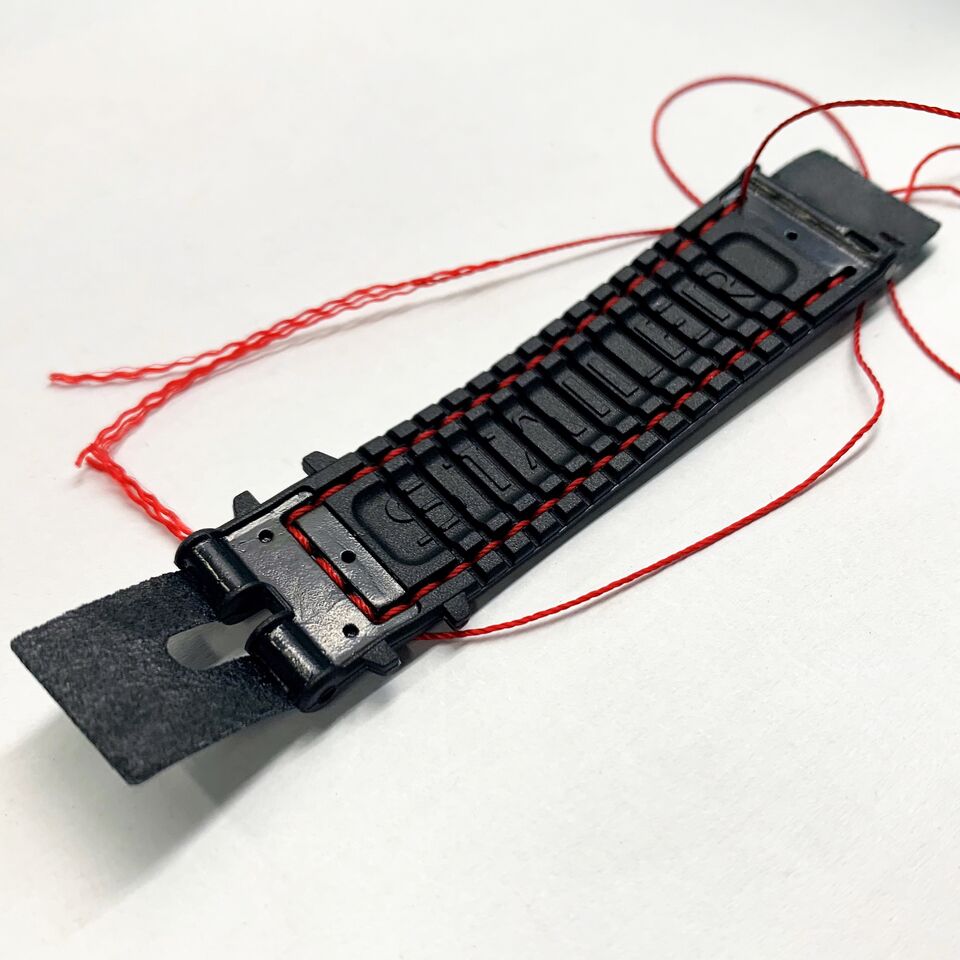
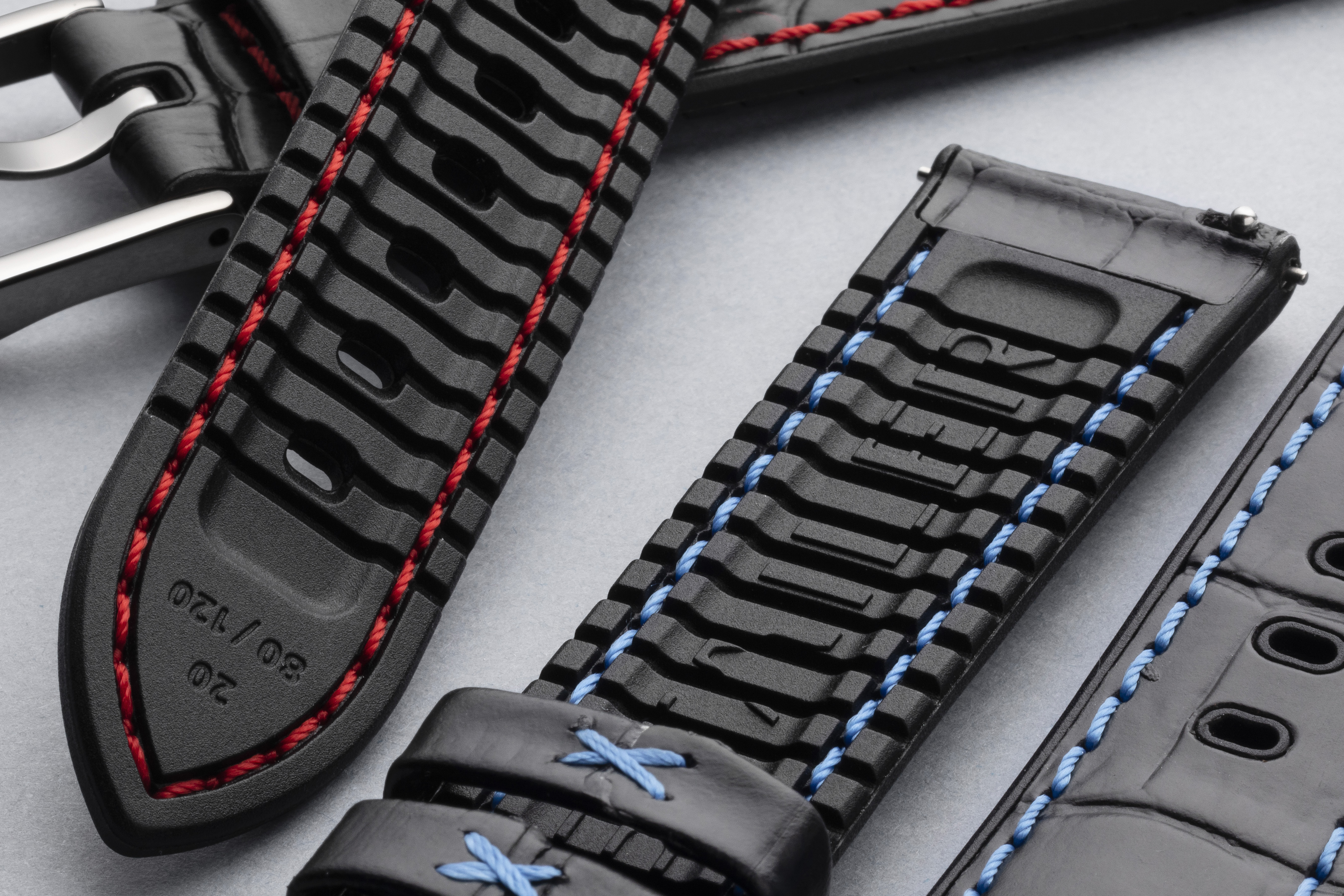
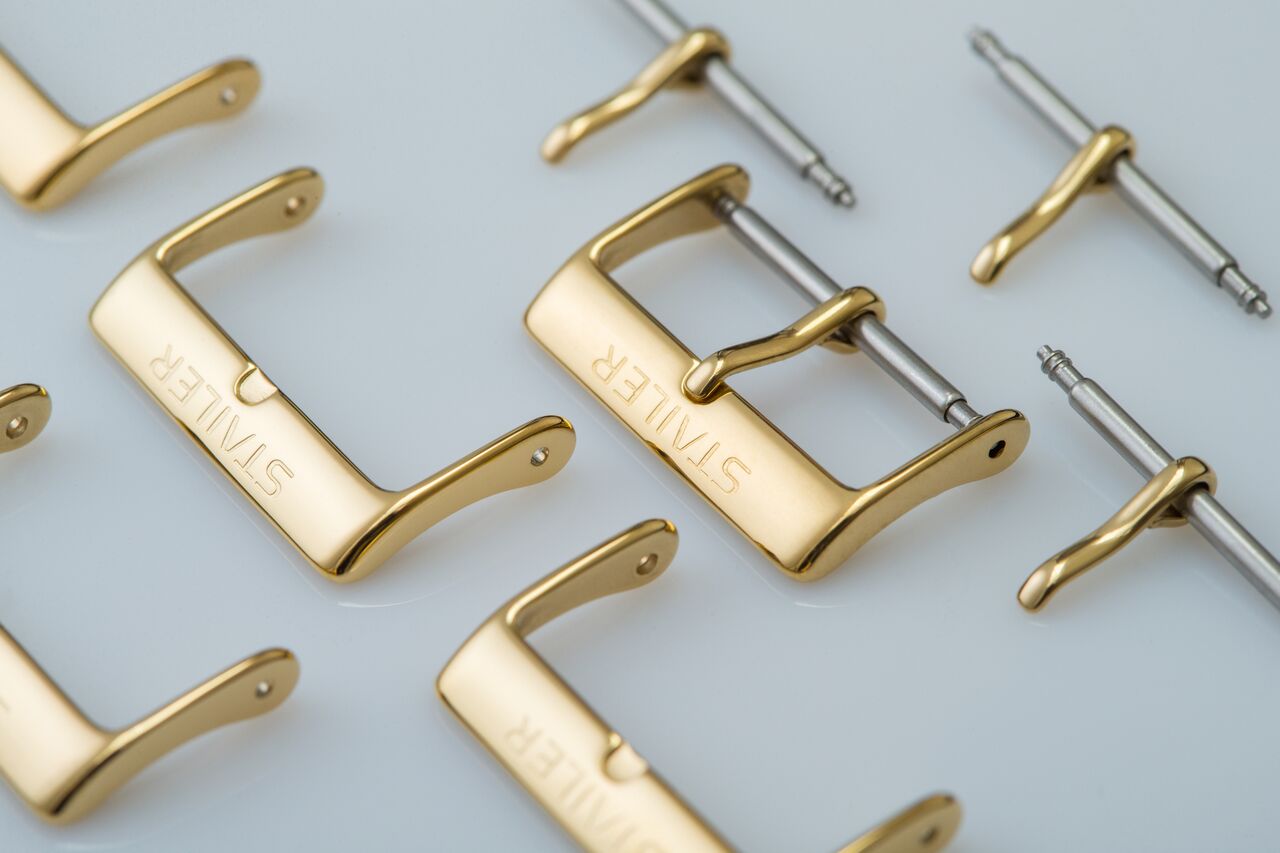

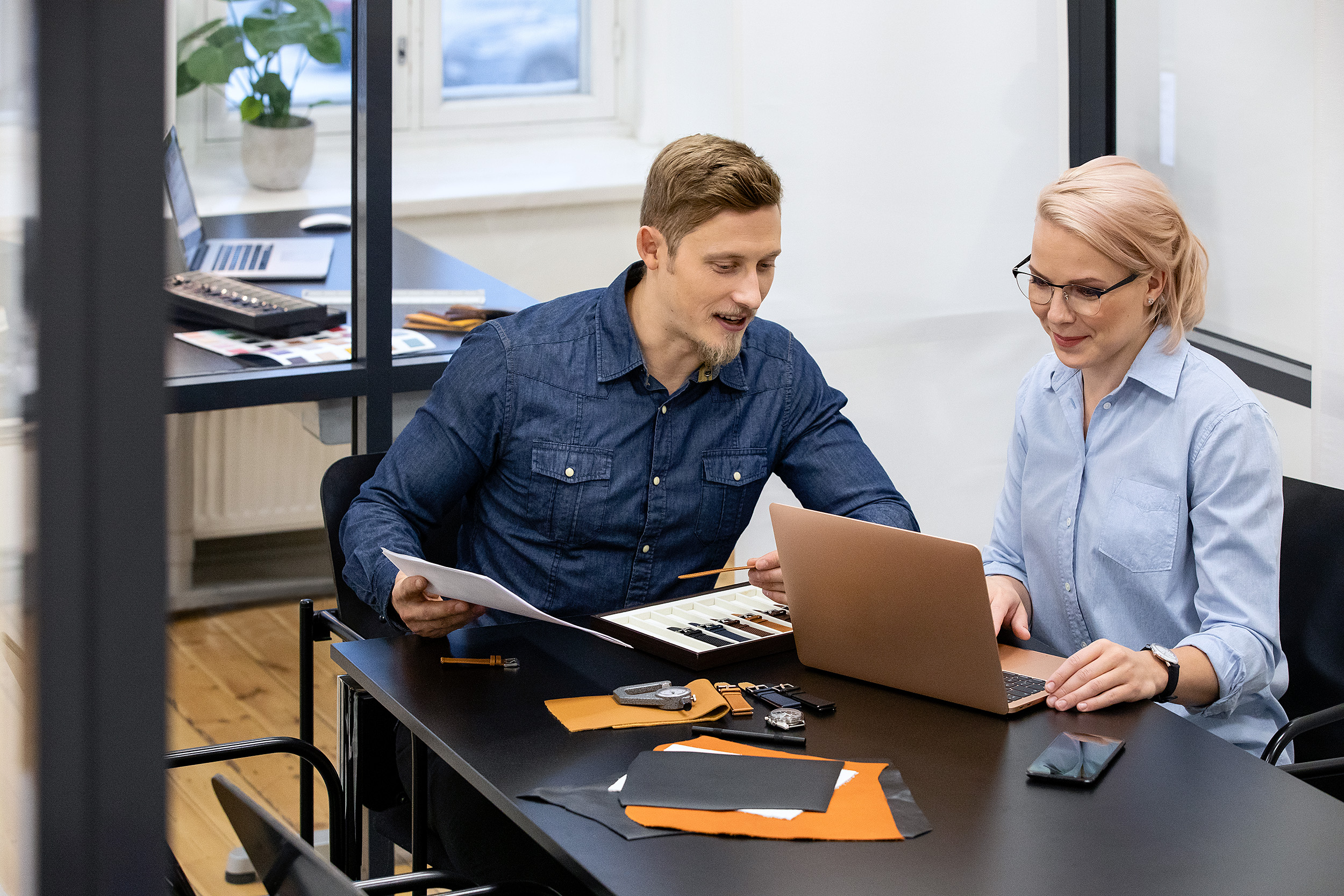
Quality control
During development and after production each model goes through a series of tests, imitating wear.
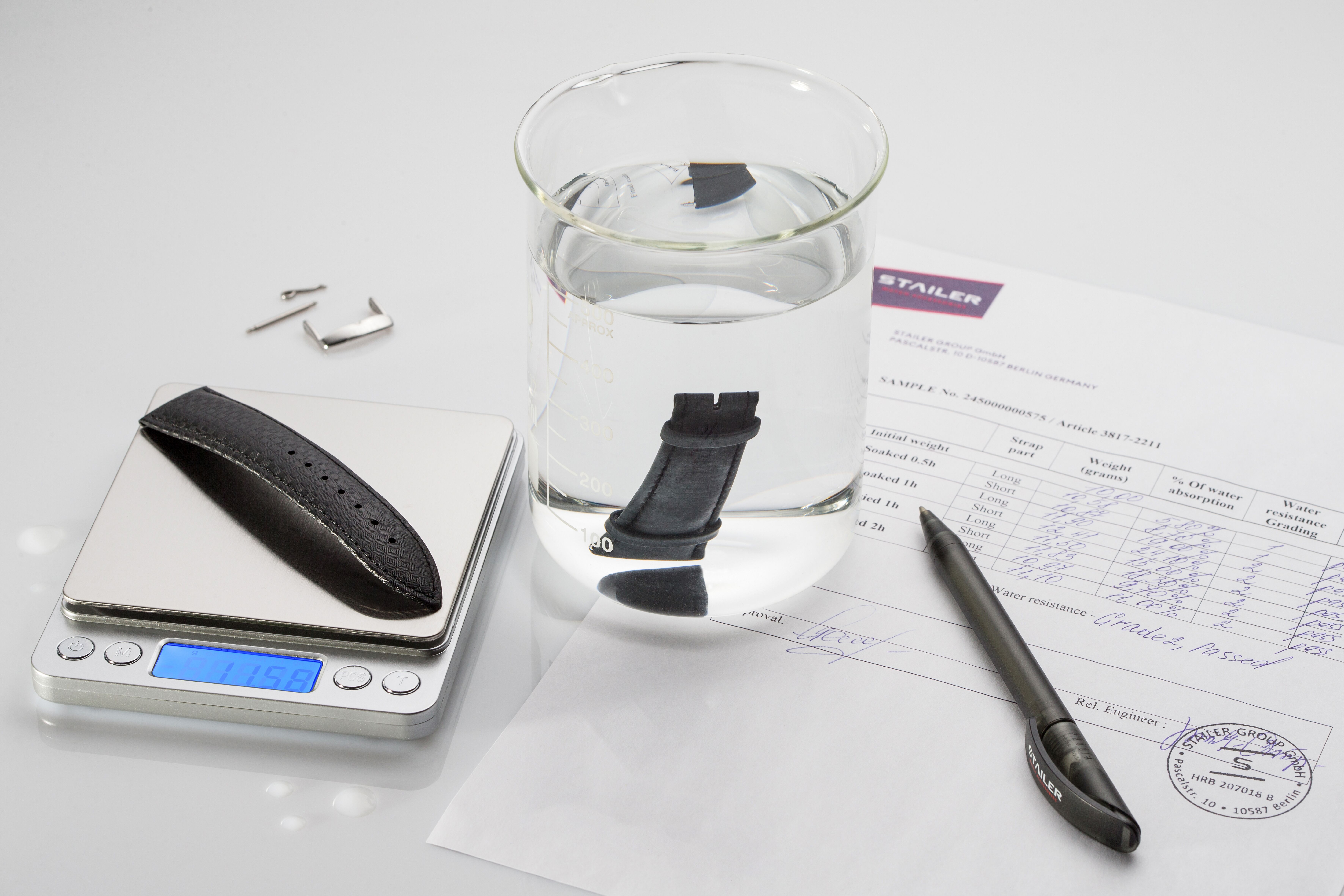
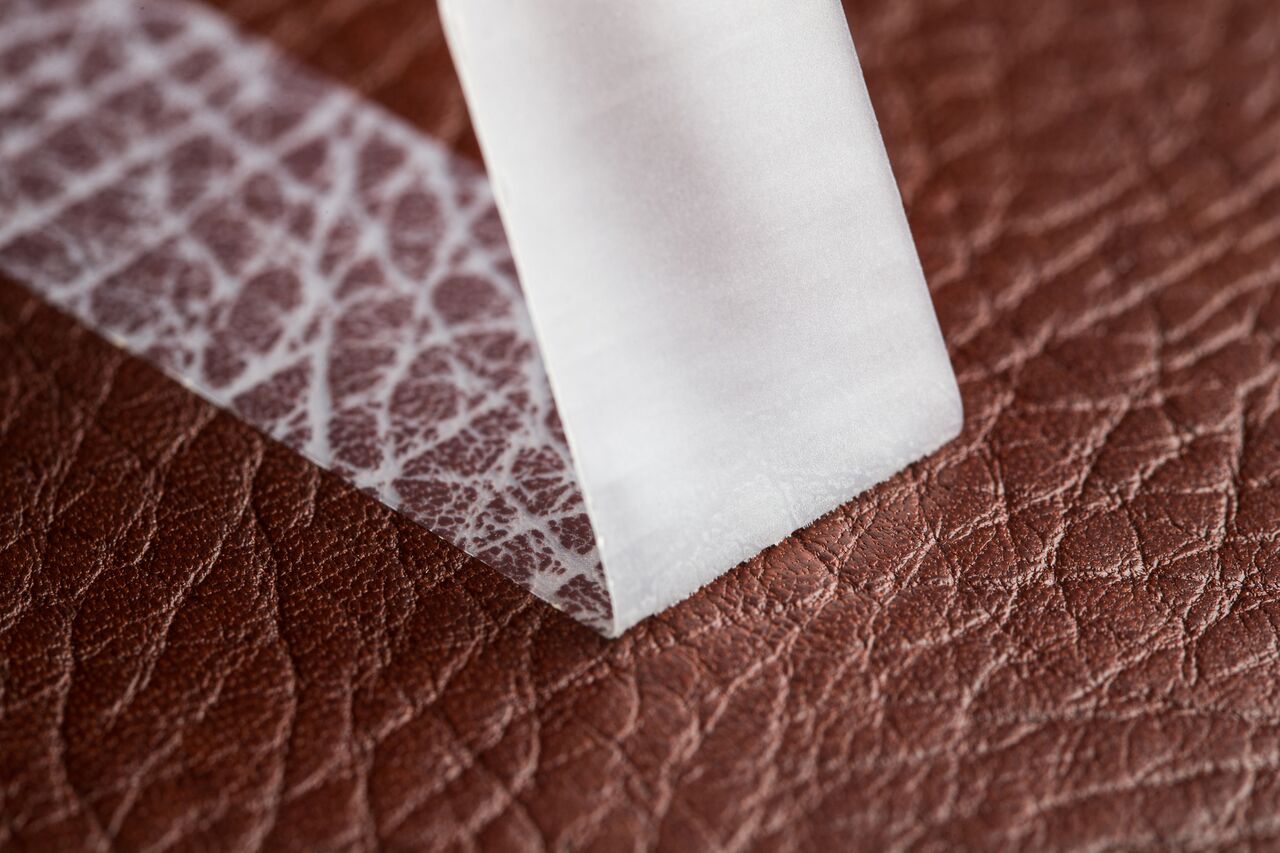
Materials
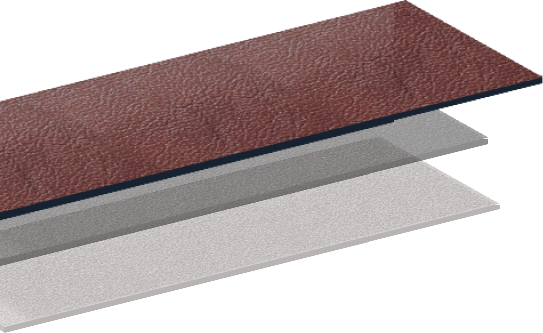
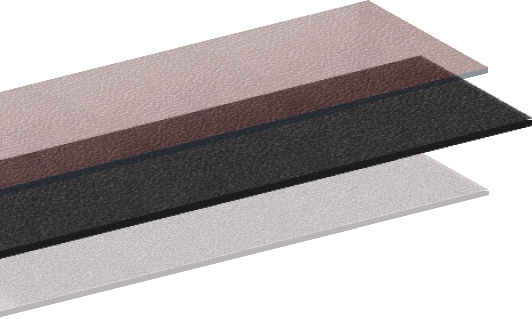
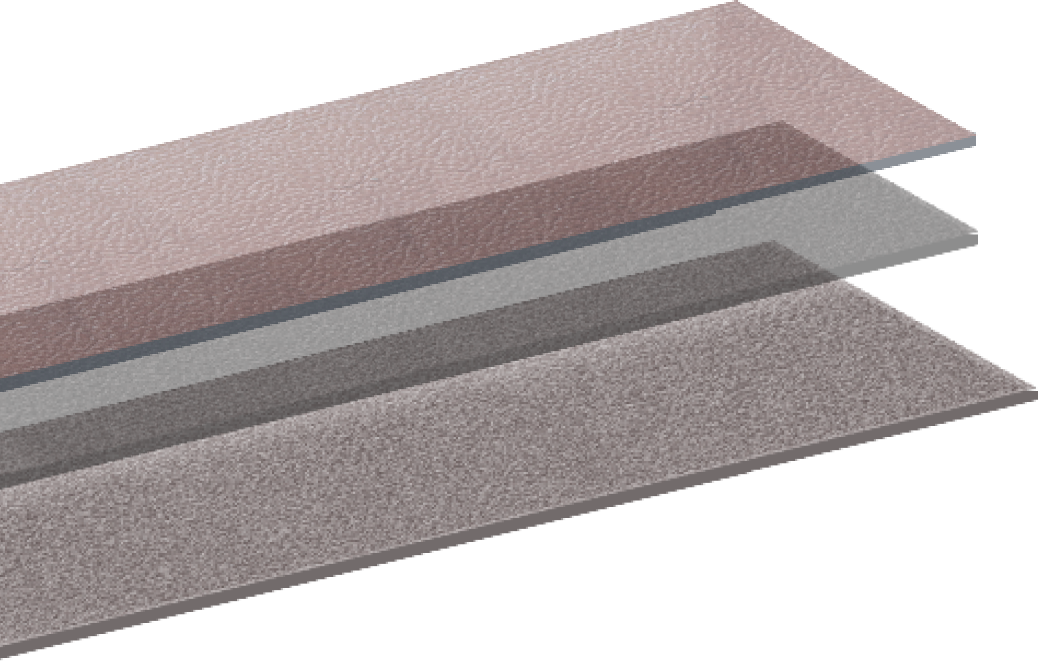
● Genuine leather is perfectly tough and elastic, but it's use is limited due to the forming complexity;
● Microfiber – a special material most closely approximating to the characteristics of genuine leather which molds well and allows to create watchstraps of complex shapes.
- Original Nubuck—classical genuine Italian leather specially tanned and brushed to enhance the material’s strikingly soft texture.
- Anfibio—specially developed leather to ensure extra wear and water resistance. Made out of EU sourced high quality Full Grain skins. Thanks to special tanning technologies it boasts pleasantly tactile texture and astonishing wear characteristics.
- Raw—the reverse side of Italian vegetable tanned leather without any extra pigment coating. Its texture feels most natural to the touch.
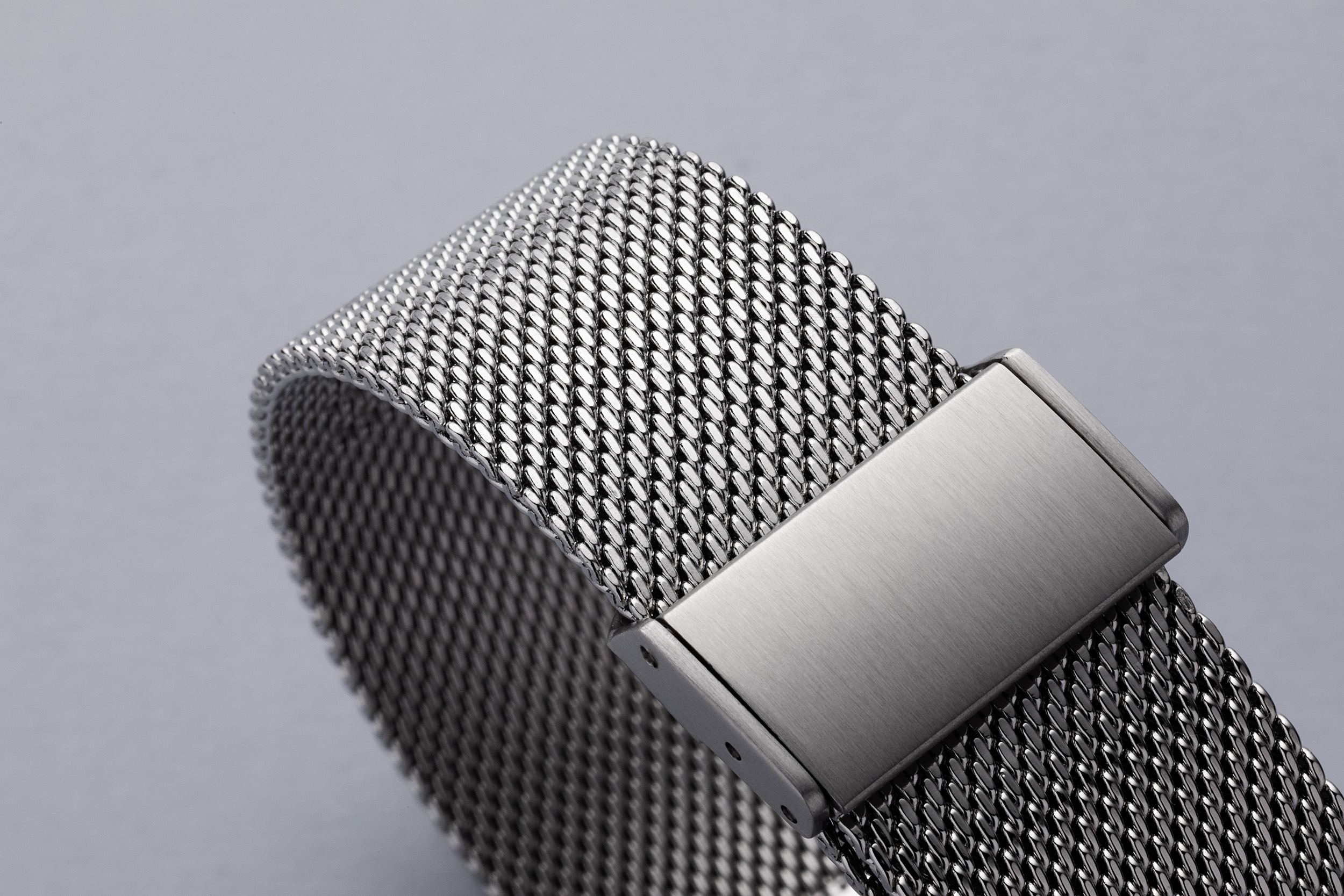
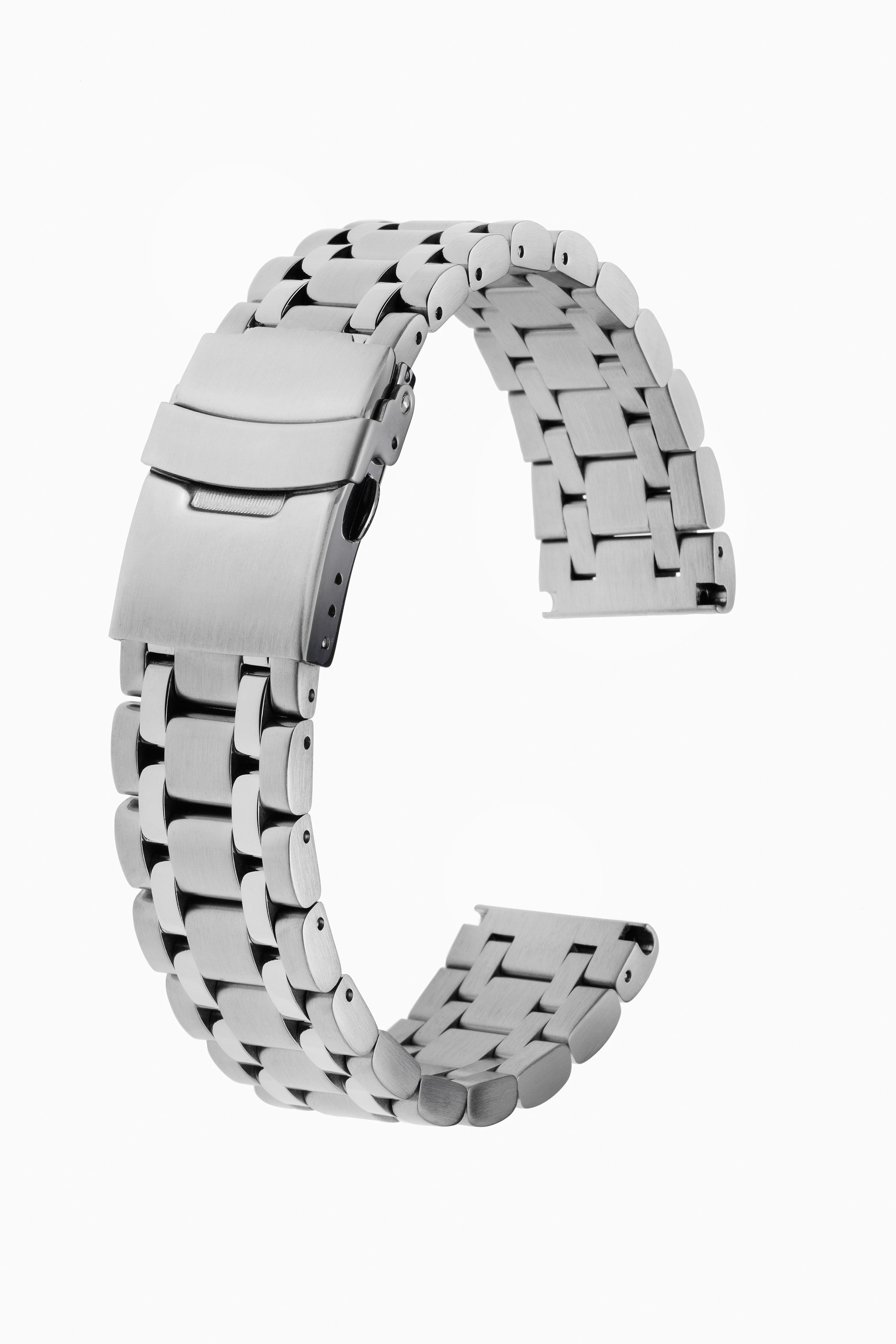
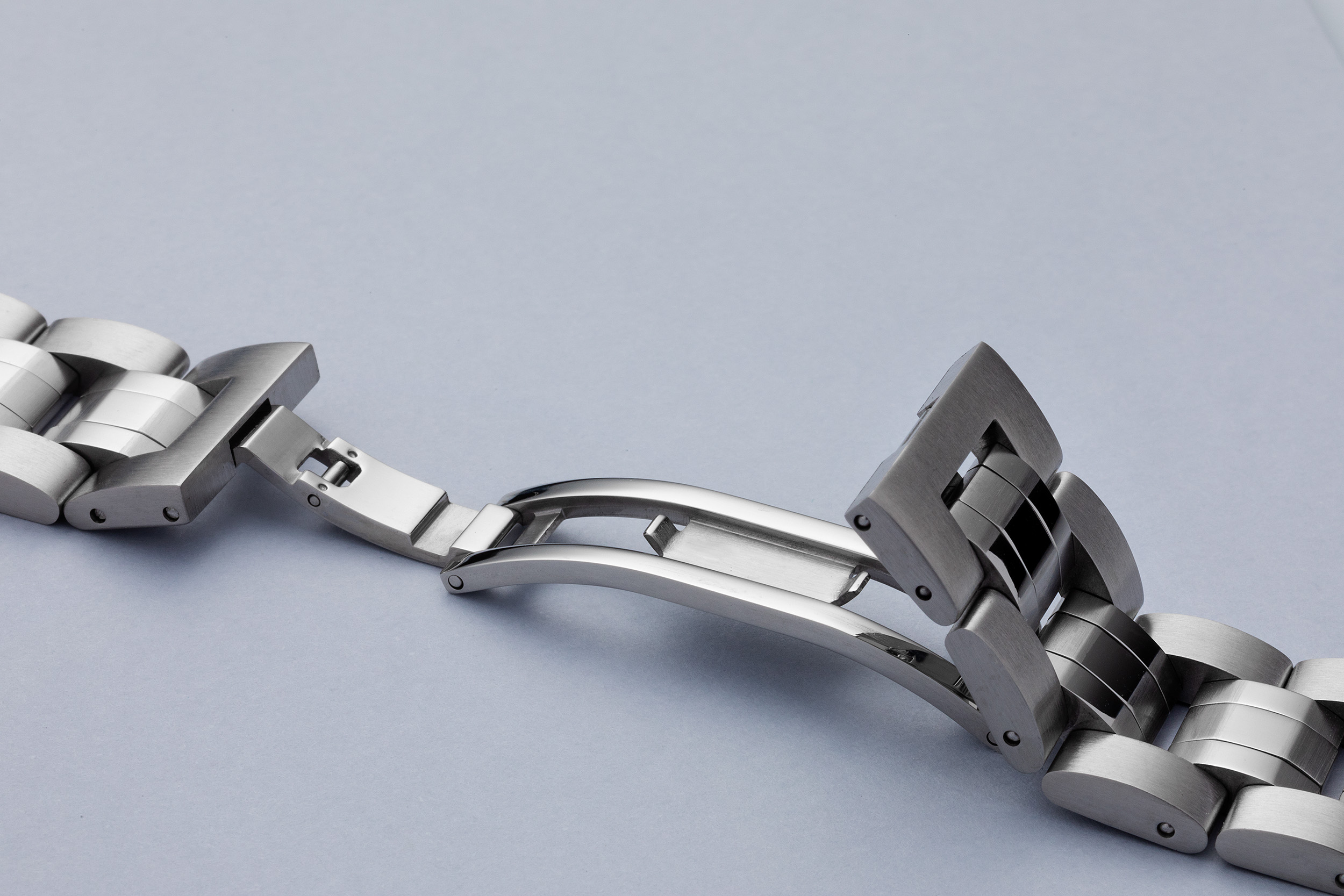
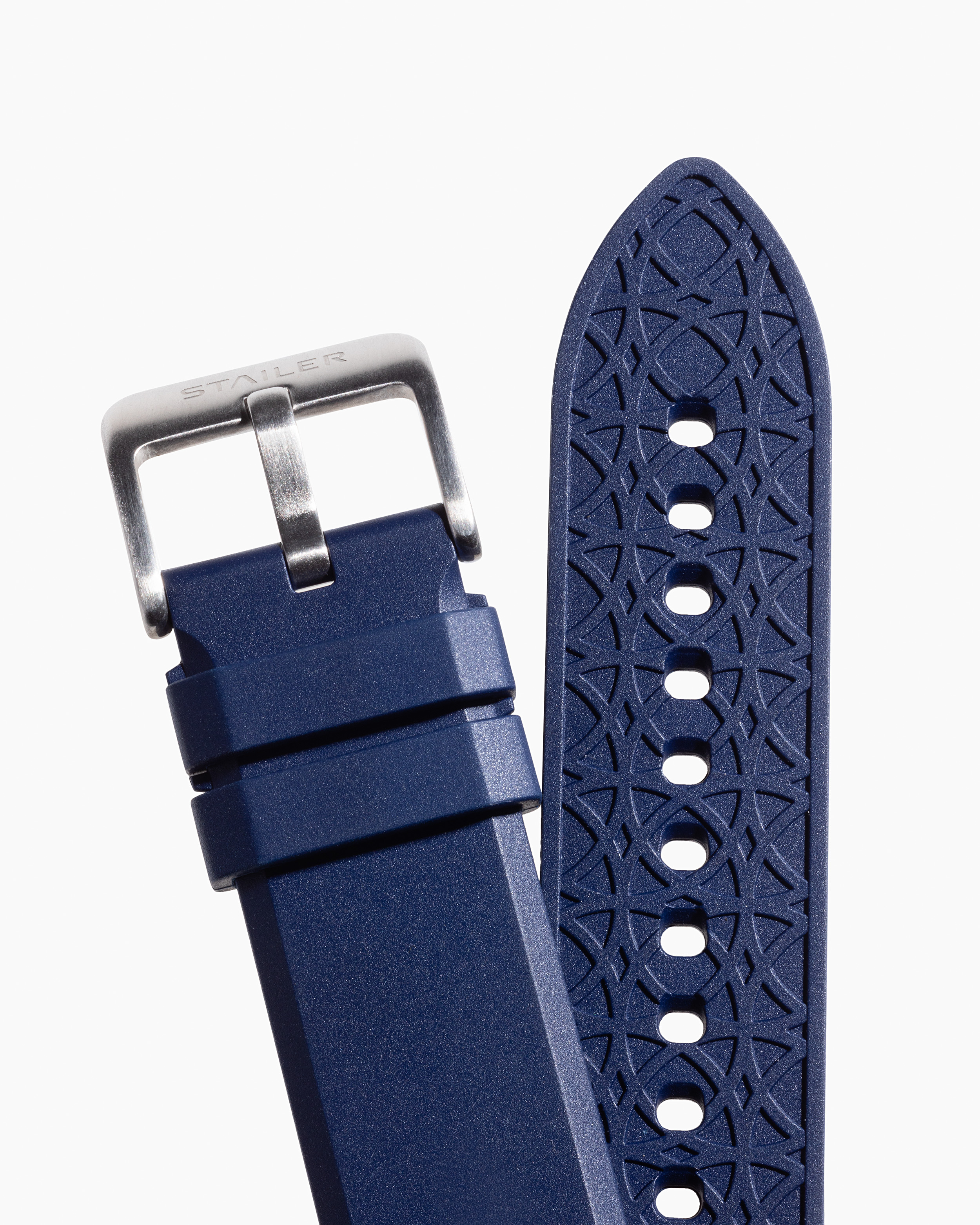
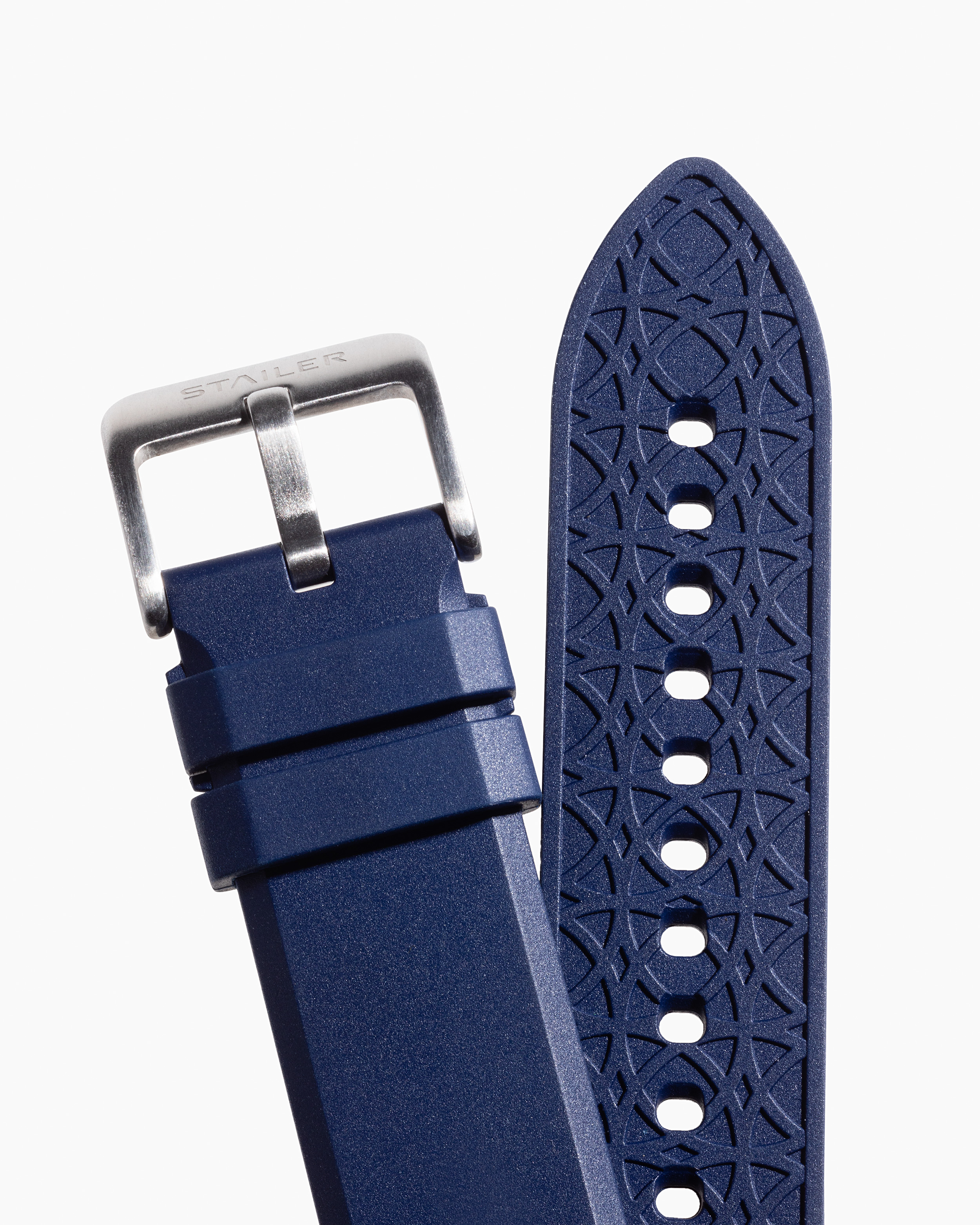
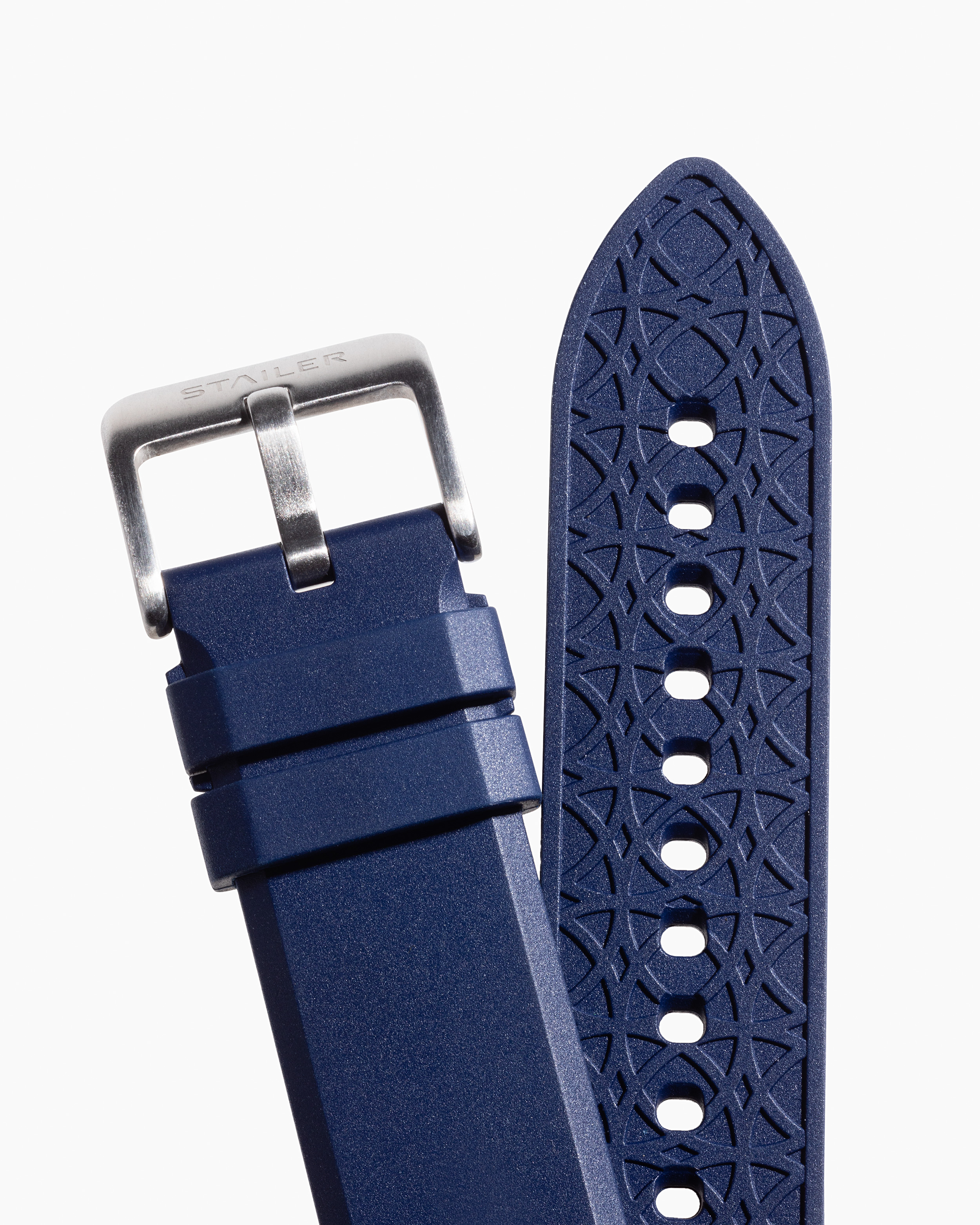
Suppliers
We use high quality materials from leading European and North American manufacturers for the production of our straps.

Straps made of HAAS leather

Straps made of Cordura Fabric

Straps made of Horween Leather

Straps made of Dani leather
